Having a mold made is a big investment for an OEM or brand owner of any size—a large enough outlay that it needs to be reliable the first time, every time. And once the tool is built and passes all tests, it’s up to the molder to ensure reliable parts are made on every cycle.
Truth be told, some molders are not able to use these tools effectively, devaluing this significant and time-intensive investment. At Performance Plastics in Cincinnati, we frequently see customers looking to transfer their molds because their previous molder couldn’t achieve production goals with the tool.
Why Transfer?
The main reason for transferring a mold comes down to the molder’s expertise. Generally, when a mold is transferred it’s because part consistency is
missing. Even if the molder makes improvements, the customer has to be able to trust its expertise and ability to solve problems right off the bat. A box of bad parts results first in a loss of confidence, followed by a lost order. There’s a saying: You only have one chance to make a good impression.
At least half of Performance Plastics’ current client relationships started out with a mold transfer, including a tool that makes 1 million critical parts per year. With the previous molder, that customer was not getting consistent production and was worried that its products would fail in the field.
The Handoff
Like so many others, that million-part customer initially reached out to Performance Plastics to discuss mold transfer. But the first step in the process actually isn’t packing the mold into a crate and shipping it to our Cincinnati offices. The first step is defining the problem.
At least half of Performance Plastics’ current client relationships started out with a mold transfer
Before a company can understand why it’s not getting the type of product that it needs, it must know what it wants out of its finished product and what it should be able to do. Ask yourself: Do you know exactly what your product is and what it offers? Do you know all of its critical operations? You
cannot have a solution without a clearly defined goal.
For example, your customer might need “Diameter A” to be perfect. However, production of the mold was driven more by another product feature.
Any qualified molder knows that it must understand what’s important to its customer and whether or not the customer is getting it out of the product. Define the problem; don’t just identify the symptoms.
Once the tool arrives, look at the project holistically and try to determine whether the problems described by the customer are related to the tooling, processing or molding capabilities of the prior molder. Review the tool completely, verifying tool steel, venting, cooling channels and any other pertinent aspects.
Once you have the mold in the press, utilize scientific injection molding principles to develop a process and set up the process-control variables to ensure that process is “locked in.” In some cases, the previous molders didn’t use a robust approach in working with the tool and just missed something. We’ve had some success at Performance Plastics identifying these types of mishaps by using our industrial computed tomography (CT) scanning equipment. By rotating the part 360° and using X-rays to create a precise 3D model, industrial CT scanning allows us to see the inner workings of a part without having to destroy it for inspection.
In addition to the application of scientific injection molding principles, use a design of experiments (DOE) to ensure you have identified the pertinent process-control variables and their limits. DOE is a branch of applied statistics that deals with the planning, conducting, analyzing, and interpreting of controlled tests to evaluate the factors that control the value of a parameter or group of parameters. At Performance Plastics, we use software that allows us to dial in and predict tolerances as they relate to process changes. DOE is a powerful data-collection and analysis tool that can be used in a variety of experimental situations. You need to know how multiple varying factors in a design interrelate and affect the results that you believe are important.
The Transfer Process
While transferring a mold from one supplier to another usually takes between two and six weeks, our experience has revealed it can actually be accomplished in as little as three days. Our engineering team works with the customer and its engineering department from the start to identify issues after the mold arrives.
At Performance Plastics, we have three in-house toolmakers that can handle mold modifications to correct errors and create fixtures and robotic end effectors if needed. In many circumstances, the prior molder and mold designer did not plan for adequate venting or they sized the mold to a poor process. After our trial runs, we are able to use our expertise in metrology to identify the best course of action.
We have a saying at Performance Plastics, “It’s not tight-tolerance unless you can measure it.” Once we know what we need to change, we work with our toolmakers to implement the plan. A lot of the timing revolves around the customer’s ability to supply its own clients. Since the mold is already in use and contracts have been signed, customers need to keep up their inventory of parts to meet demand, all while working to transfer the mold to another supplier who can use it more effectively.
We understand that it’s a painful process to transfer tools and switch suppliers. That said, we’ve handled more than 150 mold transfers over the years and know how to make the transition as seamless and painless as possible.
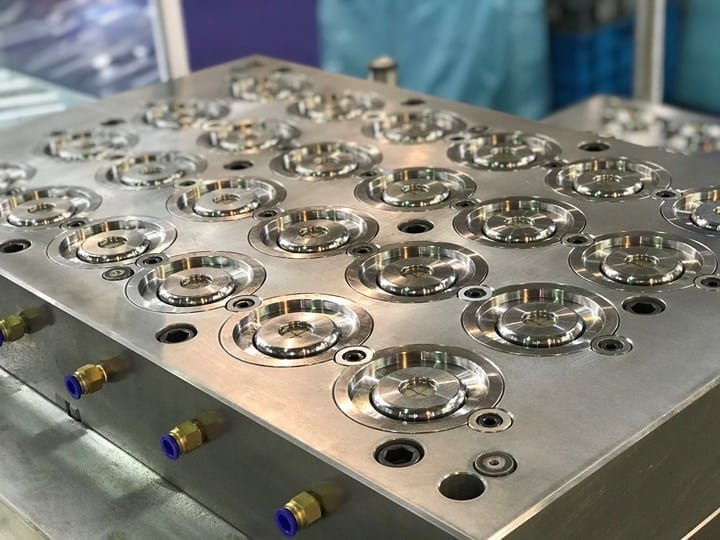
About the Authors:
Anthony Malone is VP of technology for Performance Plastics Ltd., a Cincinnati-based custom molder. With more than 25 years of experience in thermoplastics, Malone’s expertise extends into resin selection, part design and mold design. He works extensively with customers early in the product-design cycle to optimize part performance, manufacturability and life-cycle customer costs based on his extensive knowledge of advanced manufacturing techniques. Contact: [email protected].
Chris Lawson is COO of Performance Plastics and has more than 20 yr of experience with PPL. He started as a process engineer and then advanced through roles in quality, safety and manufacturing before assuming overall responsibility for operations. Lawson has specialized knowledge in the areas of automation (for production and inspection), vision systems, high-temperature polymers, process optimization and employee training. Contact: [email protected].
View Full Article in Plastics Technology Magazine